The Essential Role of a custom fastener manufacturer in Modern Manufacturing
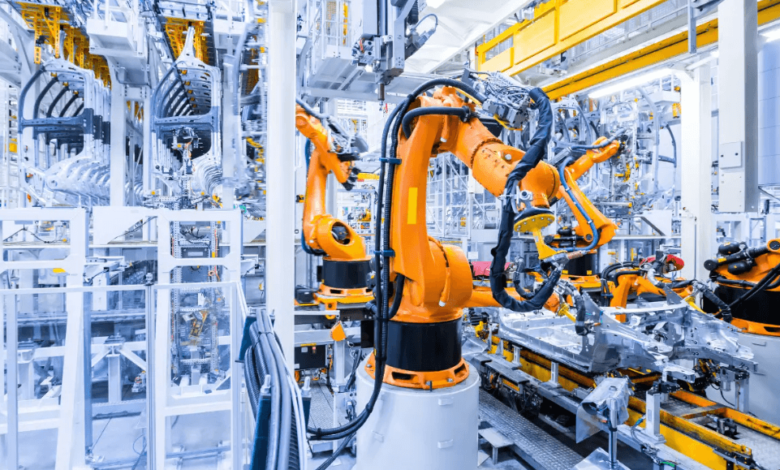
In today’s complex and fast-evolving manufacturing landscape, every component—no matter how small—plays a crucial role in product quality, performance, and safety. Among these components, fasteners are some of the most vital, serving as the glue that holds assemblies together. While standard fasteners cover a broad range of applications, there are many situations where off-the-shelf options simply don’t meet the demanding requirements of modern designs. This is where the expertise of a custom fastener manufacturer comes into play.
Whether you’re developing a new product with unique mechanical specifications or seeking to improve the durability and reliability of an existing assembly, partnering with a trusted custom fastener manufacturer can be the key to success. In this article, we’ll explore why customization in fasteners matters, what benefits come with working closely with a specialized manufacturer, and how to choose the right partner for your project.
See also: Precision CNC Turning: The Backbone of High-Accuracy Manufacturing
Why Custom Fasteners Are Becoming Increasingly Critical
Standard fasteners—like typical bolts, screws, and nuts—work well for many general applications. However, evolving technologies and stricter safety standards are pushing designers to seek fasteners that are optimized for specific performance criteria. Here are a few reasons why custom fasteners are gaining ground:
1. Unique Design Requirements
Products with unusual geometries, limited space, or special load distributions often require fasteners with tailored dimensions, shapes, or thread designs. A custom fastener manufacturer can deliver these exact specifications, ensuring seamless integration without compromising on functionality.
2. Enhanced Performance and Durability
Certain environments demand fasteners that can withstand extreme temperatures, corrosion, chemical exposure, or high fatigue cycles. By choosing specific materials, coatings, and heat treatments, a custom fastener manufacturer can create components that last longer and perform better under challenging conditions.
3. Regulatory and Industry Compliance
Medical devices, aerospace equipment, automotive parts, and food processing machinery all have strict standards governing materials, traceability, and manufacturing processes. Custom fasteners ensure compliance with these regulations, helping companies avoid costly recalls or failures.
4. Brand Differentiation
Custom fasteners allow companies to add proprietary design elements, unique markings, or special finishes that strengthen brand identity and product security. This can also help reduce counterfeiting in high-value markets.
The Capabilities of a Skilled custom fastener manufacturer
A true custom fastener manufacturer does more than simply produce parts to your blueprint. They offer expertise and services that add real value throughout the product development cycle:
Engineering Consultation
Experienced manufacturers collaborate early with clients to:
- Refine designs for manufacturability
- Select optimal materials and coatings
- Analyze load and stress requirements
- Provide CAD modeling and rapid prototyping
This reduces trial-and-error and accelerates time-to-market.
Diverse Manufacturing Techniques
Depending on the fastener type and volume, manufacturers use:
- Cold heading and thread rolling for high-volume precision parts
- CNC machining for complex or low-volume custom pieces
- Heat treatment and surface finishing like plating, anodizing, or passivation
- Quality testing including tensile strength, hardness, and fatigue analysis
Quality Control and Traceability
Top custom fastener manufacturers implement rigorous quality systems, often adhering to ISO 9001 or sector-specific standards like IATF 16949 (automotive) or AS9100 (aerospace). Each batch can be fully traceable from raw materials to finished parts, ensuring reliability and regulatory compliance.
Advantages of Partnering with a custom fastener manufacturer
Precision and Reliability
Custom fasteners meet exact specifications and performance criteria, minimizing assembly issues and improving product longevity.
Cost Efficiency in the Long Run
While custom parts might have a higher upfront cost, optimized designs reduce material waste, assembly time, and maintenance expenses over the product’s life.
Flexibility and Innovation
Manufacturers can accommodate prototype runs, design revisions, and specialized packaging. This agility supports innovation and faster iteration cycles.
Competitive Edge
Unique fasteners help differentiate products and demonstrate a commitment to quality, which can be a significant factor in winning contracts and customer loyalty.
Selecting the Right custom fastener manufacturer: What to Look For
To ensure your project’s success, it’s critical to evaluate potential suppliers thoroughly:
Criteria | What to Assess |
Experience and Industry Focus | Years in business, familiarity with your sector (medical, automotive, aerospace, etc.) |
Technical Expertise | Availability of engineering support, prototyping capabilities, and material knowledge |
Manufacturing Capabilities | Range of techniques (cold heading, CNC), volume flexibility, tooling options |
Quality Certifications | ISO 9001, IATF 16949, AS9100, and other relevant certifications |
Materials and Finishes | Availability of specialized alloys and coating processes |
Communication and Support | Responsiveness, language skills, project management tools |
Delivery and Logistics | Reliability, packaging standards, international shipping experience |
Request references, samples, and case studies to validate the supplier’s claims. Whenever possible, visiting the manufacturing facility or arranging virtual tours offers deeper insights.
Real-World Example: How Custom Fasteners Elevated a Product’s Performance
A European manufacturer of precision optical equipment required fasteners that could maintain stable clamping force despite temperature fluctuations and vibration. Standard fasteners failed due to thermal expansion and loosening.
By collaborating with a custom fastener manufacturer, they developed:
- Fasteners made from an Invar alloy with minimal thermal expansion
- Custom thread-locking geometry to resist vibration-induced loosening
- Surface treatments for corrosion resistance in cleanroom environments
The result was a significant increase in product reliability, fewer service calls, and enhanced customer satisfaction.
Future Trends in Custom Fastener Manufacturing
Advanced Materials
Research into lightweight and high-strength materials like titanium alloys and composites is expanding the capabilities of custom fasteners.
Additive Manufacturing
3D printing enables rapid prototyping and complex designs previously impossible with traditional methods, speeding innovation.
Smart Fasteners
Embedded sensors to monitor torque, stress, or temperature are emerging, providing real-time data for predictive maintenance.
Sustainability Focus
Eco-friendly materials, recyclable coatings, and waste reduction during manufacturing are becoming priorities for manufacturers and clients alike.
Conclusion
In an era where product quality and innovation define market leaders, the role of a custom fastener manufacturer is indispensable. Custom fasteners not only meet specific design and performance demands but also contribute to overall product reliability, safety, and customer trust.
By partnering with a knowledgeable and capable manufacturer, companies gain access to engineering expertise, advanced manufacturing processes, and stringent quality assurance—essentials for thriving in competitive markets.
Investing in the right custom fastener manufacturer is not just about securing parts—it’s about building a foundation for success, innovation, and sustained growth.