Precision CNC Turning: The Backbone of High-Accuracy Manufacturing
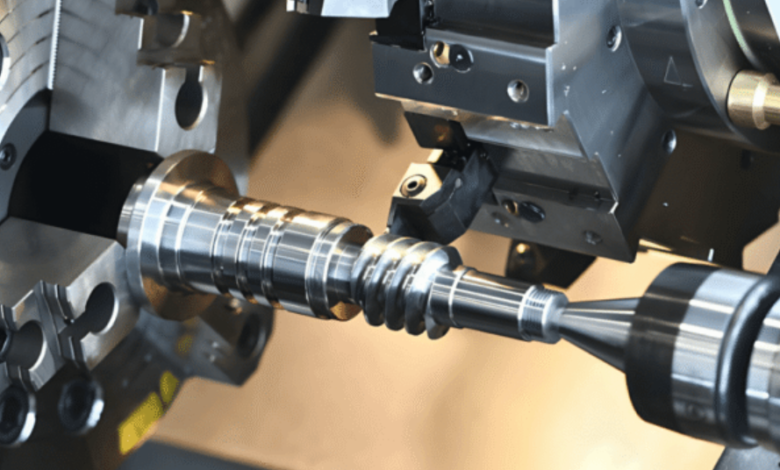
In the world of modern manufacturing, where tolerances are measured in microns and components must meet exacting specifications, precision CNC turning stands out as a critical machining method. From aerospace to medical devices and automotive components, this technology ensures that parts are produced with unmatched accuracy, repeatability, and speed. As industries demand more complex and tighter-tolerance parts, manufacturers are turning to precision CNC turning to meet those expectations efficiently.
This article explores what precision CNC turning is, how it works, its key benefits, industries that rely on it, and the innovations shaping its future.
What Is Precision CNC Turning?
Precision CNC turning is a subtractive manufacturing process where a computer numerically controlled (CNC) lathe is used to remove material from a rotating workpiece to form a specific shape. What distinguishes “precision” CNC turning from conventional turning is the level of exactitude it delivers—typically within ±0.005 mm or even tighter, depending on the equipment and process control.
It involves automated machinery guided by advanced CAD/CAM software that produces consistent results on even the most complex parts. In precision turning, the cutting tools are set with digital accuracy, ensuring every piece meets strict dimensional and surface finish standards.
See also: Editing for Narrative Storytelling: Tools and Techniques
How the Precision CNC Turning Process Works
- Design & Programming
It all starts with a 3D CAD model, which is then converted into a machine-readable G-code. This code guides the CNC lathe in every step—from tool movement to spindle speed. - Material Preparation
Raw cylindrical stock—usually metal or high-performance plastic—is loaded into the lathe, often with automatic feeding systems for continuous runs. - Turning Operation
The lathe rotates the workpiece while the cutting tools perform multiple operations: facing, tapering, threading, grooving, and more. Advanced machines can turn both ends using dual spindles. - Post-Processing & Inspection
After machining, parts may undergo deburring, surface treatments, or heat treatment. Inspection tools like coordinate measuring machines (CMMs) are used to verify tolerances.
What Makes CNC Turning “Precision”?
Several key factors differentiate precision CNC turning from standard operations:
- Ultra-fine tool movement control (up to 0.001 mm)
- Stable machine bases that reduce vibration
- Closed-loop feedback systems
- Precision-ground spindles and ball screws
- Automated tool calibration
These technical features combine to produce parts that are accurate to tolerances required in critical applications.
Advantages of Precision CNC Turning
1. High Dimensional Accuracy
Precision CNC turning delivers components with micro-level tolerances, which are essential in sectors where performance depends on flawless fit and function.
2. Repeatability Across Batches
Whether you’re producing 10 or 10,000 units, the last part will be as accurate as the first, ensuring consistent quality over long production runs.
3. Fast Turnaround Time
Thanks to automation and minimal human intervention, precision CNC turning greatly reduces the time it takes to move from design to finished product.
4. Lower Waste and Greater Efficiency
With optimized tool paths and precise control, material waste is minimized, which leads to cost savings in raw material and better sustainability.
5. Complex Geometries Made Easy
CNC turning centers can easily produce parts with intricate contours, internal bores, threads, and tapers that are difficult to achieve manually.
Key Applications of Precision CNC Turning
Aerospace Components
Flight-critical parts like turbine housings, engine shafts, and sensor enclosures need ultra-precise machining. Even the smallest dimensional error can result in catastrophic failure.
Medical Devices
Surgical instruments, orthopedic implants, and dental tools often require highly specific materials and finishes—both of which precision CNC turning can deliver.
Automotive Industry
Parts such as pistons, drive shafts, bushings, and gear components need consistent tolerances to ensure vehicle performance and safety.
Electronics and Semiconductors
Precision CNC turning is used to manufacture connector pins, miniature housings, and thermal management components that fit into circuit boards and electronic enclosures.
Oil & Gas Equipment
Valves, pressure regulators, and rotating seals require tight tolerances to function in extreme environments—often achieved through precision CNC turning.
Precision CNC Turning Machines
Modern turning centers can vary from basic 2-axis machines to highly advanced multi-axis machines. Below are the types commonly used in precision turning:
- 2-Axis Lathes: Suitable for basic cylindrical and conical geometries.
- Multi-Axis CNC Turning Centers: Machines with 3 to 9 axes are used for parts with cross-drilled holes, slots, and compound angles.
- Swiss-Type Lathes: Ideal for producing long, slender parts with high precision (e.g., bone screws, watch components).
- Twin-Spindle Machines: These allow for simultaneous machining on both sides, enhancing speed and accuracy.
Challenges in Precision CNC Turning
Despite its many advantages, precision CNC turning does come with some challenges:
⛔ High Setup Cost
Initial investments in machinery and software can be significant, though they are offset by long-term gains in productivity and accuracy.
⛔ Skilled Labor Requirement
Operating and programming precision CNC machines require highly trained machinists or engineers familiar with CAD/CAM systems.
⛔ Tool Wear
With tight tolerances, even the slightest tool wear can affect part quality. Continuous monitoring and preventive maintenance are essential.
Future Trends in Precision CNC Turning
✅ Automation and Robotics
Machine-tending robots are increasingly used to feed materials and change tools, further reducing cycle times and human error.
✅ AI-Powered Machining
Artificial Intelligence is being applied to optimize tool paths, predict maintenance needs, and adapt machining parameters in real-time.
✅ IoT and Industry 4.0
Smart factories are integrating CNC machines into cloud-based networks for real-time monitoring, data analytics, and remote control.
✅ Eco-Friendly Machining
Coolant recycling, low-emission cutting tools, and energy-efficient motors are making precision CNC turning more sustainable.
Choosing the Right Precision CNC Turning Partner
Selecting the right manufacturing partner is crucial to getting the most from precision CNC turning. Here are key factors to consider:
- Certifications: Look for ISO 9001, AS9100, or medical certifications if applicable.
- Material Expertise: Ensure the supplier can work with metals like titanium, stainless steel, and aluminum, or engineering plastics.
- Turnaround Time: Quick lead times without compromising quality are essential for meeting market demands.
- DFM Capabilities: Design for Manufacturability support can improve part design and reduce costs.
Conclusion
Precision CNC turning is not just a manufacturing process—it’s a strategic capability that supports innovation, quality, and competitiveness in countless industries. Whether you’re building mission-critical aerospace components or miniature medical parts, the demand for accuracy and consistency has never been higher. Precision CNC turning offers a perfect blend of speed, accuracy, and flexibility, making it indispensable in the world of high-performance manufacturing.
Investing in this technology—whether in-house or through a trusted partner—ensures that your products meet the most rigorous quality standards, ready to compete in a global marketplace.