Common Issues in Mechanical Systems and How to Address Them
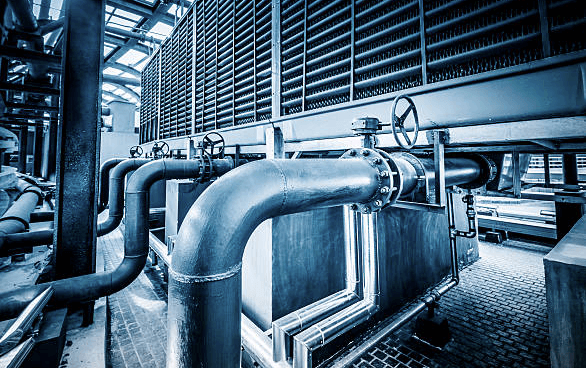
Mechanical systems play a crucial role in various industries—powering operations, ensuring efficiency, and maintaining productivity. However, like any complex system, they are prone to wear and tear, leading to reduced performance, costly downtimes, and potential safety risks.
This blog explores some of the most common issues encountered in mechanical systems and the steps you can take to fix or prevent them. Whether you’re managing an industrial gearbox or troubleshooting a conveyor belt, understanding these challenges can save you both time and money.
Causes of Common Mechanical Failures
1. Wear and Tear
Mechanical components naturally degrade over time due to friction, temperature changes, and repetitive use. Factors like poor lubrication, improper material use, or misalignment can accelerate this process.
Solution:
- Routine Maintenance: Regular inspections can identify early signs of wear. Replace worn-out parts promptly.
- Lubrication: Ensure proper lubrication of moving parts to reduce friction and heat.
- Material Selection: Use durable, wear-resistant materials suitable for the task and environment.
2. Misalignment
Misalignment occurs when parts of a system—such as shafts, belts, or chains—are out of sync. This can lead to increased wear, vibrations, and energy loss.
Solution:
- Precision Installation: During setup, ensure all components are aligned correctly.
- Alignment Tools: Use laser alignment or other advanced tools to correct misaligned components.
- Check for Loose Bearings: Loose or worn bearings can throw off alignment, so inspect and replace them as necessary.
3. Vibration Issues
Vibrations in mechanical systems can be caused by loose parts, imbalance in rotating components, or structural instability. Left unchecked, vibrations can damage machinery and reduce its lifespan.
Solution:
- Dynamic Balancing: For rotating machinery, ensure proper weight distribution to minimize imbalance.
- Secure Fasteners: Tighten bolts, nuts, and screws that may have loosened over time.
- Structural Checkups: Assess the machinery’s foundation and adjust if there are stability issues.
4. Overheating
Mechanical systems generate a substantial amount of heat, and without proper cooling mechanisms, overheating can lead to system shutdown or permanent component damage.
Solution:
- Cooling Systems: Install effective cooling methods, such as fans, heat sinks, or liquid cooling systems.
- Temperature Sensors: Use sensors to monitor heat levels and preemptively act.
- Proper Ventilation: Ensure the operating environment has adequate airflow to dissipate heat.
5. Contamination
Contamination occurs when external particles, such as dirt, dust, or debris, enter mechanical systems. Contaminants can interfere with operations and degrade sensitive components.
Solution:
- Sealed Systems: Invest in sealed designs to minimize exposure to external particles.
- Air Filters and Screens: Regularly clean or replace air filters and other protective screens.
- Environment Control: Operate the machinery in clean environments when feasible.
Addressing Gearbox Failures
One critical component often affected by mechanical challenges is the industrial gearbox—the powerhouse behind heavy-duty machines. Gearboxes face vulnerabilities like overheating, gear misalignment, and lubrication failure.
Solutions Specific to Gearboxes:
- Ensure Proper Lubrication: Gearboxes require consistent lubrication to handle friction and load pressures effectively.
- Analyze Load Capacity: Overloading gearboxes can lead to premature damage. Always operate within the recommended load limits.
- Use Vibration Analysis: Monitor vibrations within the gearbox to identify potential issues such as gear misalignment or loosened bolts.
A robustly-maintained industrial gearbox contributes significantly to overall system efficiency, so paying attention to its specific needs is critical.
Preventative Maintenance Tips
Preventative measures are the lifeblood of efficient mechanical systems. Here’s how you can keep your systems running smoothly:
Create a Maintenance Schedule
Develop a maintenance plan tailored to each machine’s operational needs. Stagger inspections and maintenance tasks to avoid long downtimes.
Implement Condition Monitoring
Use sensors and IoT tools to monitor real-time data, such as temperature, vibration, and pressure. These insights can predict when maintenance is needed, reducing unexpected failures.
Train Operators
Ensure machine operators are well-trained to manage everyday use and spot early warning signs of system degradation.
See also Cybersecurity Services for Digital Security and Data Protection
When to Seek Professional Help
Not every issue can or should be resolved in-house. For complex problems, consult industry experts who specialize in mechanical system diagnostics and repairs. Many service providers offer advanced testing and repair solutions that can extend the lifespan of your equipment and optimize operations.
If you’re investing in costly machinery, consider partnering with a professional maintenance service to keep your equipment in peak condition regularly.
Why Knowing These Issues Matters
Mechanical system problems affect efficiency, safety, and your bottom line. By understanding common failures—like wear and tear, alignment issues, or contamination—you’ll be better equipped to address these proactively. The key to avoiding costly aftereffects lies in a well-thought-out maintenance plan, with targeted efforts to identify and eliminate root causes early on.
If you’re facing specific challenges around systems like gearboxes, remember that industry-specific solutions, like alignment or lubrication checks, can make a difference.