The Role of Pigging System in Paint Industry: A Sustainable Shift in Production Efficiency
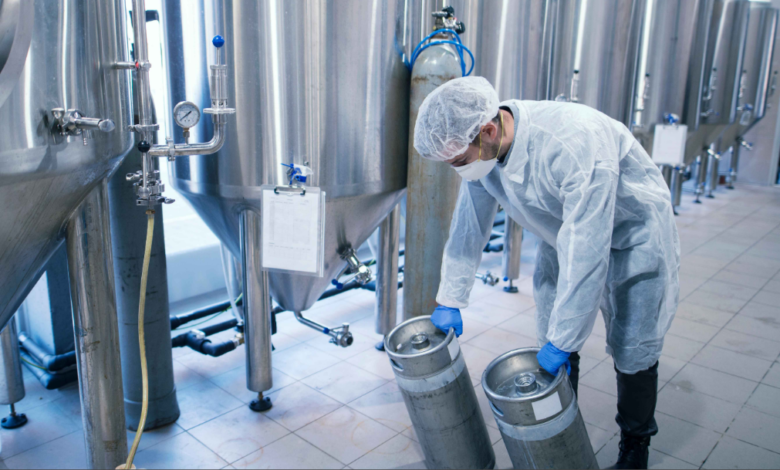
In the world of paints and coatings, precision, cleanliness, and waste reduction are essential. The highly competitive paint sector—be it decorative, automotive, industrial, or protective coatings—faces ever-growing pressure to deliver more output with less waste, fewer cleaning chemicals, and reduced production downtime. In this pursuit, the implementation of a pigging system in paint industry has emerged as a transformative solution.
Pigging systems are now becoming a key strategy in streamlining production lines, reducing losses, improving product recovery, and boosting sustainability credentials. This article explores the necessity, benefits, and best practices associated with using a pigging system in paint industry operations.
Understanding the Pigging Concept
Before diving into how pigging integrates into paint production, it is important to grasp what pigging is. Pigging is a technique where a specially designed projectile—known as a pig—is pushed through a pipeline. The pig moves through the pipe, removing and recovering any residual product, separating batches, and cleaning the pipeline in the process.
The technology is used across multiple sectors, including food, beverage, cosmetics, chemicals, and more recently, paint manufacturing. In essence, a pigging system in paint industry ensures that paint left inside process pipelines after batch production is recovered rather than wasted or flushed away.
See also: Why PCredCom Is Mexico’s Favorite Tech Playground
Why the Paint Industry Needs Pigging Systems
The unique characteristics of paint—high viscosity, pigmentation, color sensitivity, and solvent content—make the industry a perfect candidate for pigging. Traditional methods of flushing pipelines with solvent or water after each batch can be wasteful, slow, and environmentally harmful. Here’s where pigging comes in:
1. Product Recovery
In paint manufacturing, even small quantities of unrecovered paint can accumulate into significant losses. A pigging system can recover up to 99.5% of the paint remaining in the pipeline after a production run. For high-value coatings, this can mean thousands of liters saved annually.
2. Color Changeovers
Paint producers frequently switch between different color batches. Without a pigging system, this would require full pipeline flushing using solvents, generating hazardous waste and increasing downtime. A pigging system allows a clean and efficient separation between different paint colors.
3. Reduced Cleaning Requirements
Flushing paint lines with cleaning agents or solvents is time-consuming and expensive. A pigging system significantly reduces the volume of chemicals needed for cleaning, minimizing both costs and the plant’s environmental footprint.
4. Shorter Downtime
Manual cleaning or excessive flushing delays production. Implementing a pigging system in paint industry lines enables quicker batch changes and faster returns to operation, improving overall equipment effectiveness (OEE).
5. Environmental Compliance
The paint industry is under constant scrutiny due to VOC (volatile organic compound) emissions, water usage, and hazardous waste generation. A pigging system helps meet regulatory standards by reducing solvent use and minimizing waste discharge.
Components of a Pigging System in Paint Applications
A standard pigging system in paint industry applications typically includes:
- Pig Launcher: The entry point where the pig is inserted into the pipeline.
- Pig Receiver: The collection chamber at the other end of the pipeline.
- Pig: A specialized projectile made of hygienic and chemically resistant materials, designed to push paint through the pipeline and scrape internal surfaces.
- Pig Detection Sensors: These devices track the pig’s position in real time, ensuring system control and safety.
Implementation Considerations
To successfully install a pigging system in paint industry settings, certain factors must be taken into account:
1. Pipeline Design
Pigging systems work best with straight, smooth pipelines. However, modern pigs can navigate bends and elevation changes if properly designed. Material compatibility with solvents, resins, and pigments must also be considered.
2. Product Characteristics
Viscosity, drying time, chemical reactivity, and solid content all influence system design. For instance, paints that cure quickly must be moved through the system before setting.
3. System Integration
Automated systems allow for seamless pigging cycles, often integrated into a facility’s SCADA or PLC. This enables predictive maintenance, efficient cleaning cycles, and minimal manual intervention.
4. Regulatory Compliance
Paint manufacturing often involves flammable or hazardous substances. Pigging systems must meet ATEX or equivalent safety certifications in explosive or solvent-heavy environments.
Return on Investment (ROI) of Pigging in Paint
While installing a pigging system requires upfront investment, the long-term savings are significant. Here’s how ROI is typically achieved:
- Increased product yield
- Lower solvent purchase and disposal costs
- Reduced labor hours for cleaning
- Fewer hours of downtime between batches
- Regulatory cost savings due to lower emissions and waste
Most paint manufacturers see payback within 6 to 18 months depending on production scale and frequency of product changeovers.
Real-Life Case Study
A mid-sized paint producer in South Asia implemented a pigging system in paint industry operations for its solvent-based coatings. The company had long struggled with high solvent use, color cross-contamination, and changeover time between custom paint shades.
Results after implementation:
- Paint recovery increased by 94%
- Solvent usage dropped by 68%
- Cleaning time cut from 50 minutes to 12 minutes
- Annual savings exceeded $120,000 in product and solvent costs
The pigging system paid for itself within 10 months and has since been expanded to other production lines.
Conclusion
The pigging system in paint industry is not merely an operational upgrade—it is a business-critical tool that enhances productivity, reduces environmental impact, and supports high-quality manufacturing practices. As customer demands grow and regulatory pressures increase, more manufacturers are turning to pigging to stay competitive.
By investing in a well-designed pigging system, paint producers can expect better batch control, faster turnarounds, reduced waste, and improved bottom-line performance. It’s a win for business, customers, and the environment alike.